TS-BASE 受発注
2024.02.27
出荷の流れを解説!生じやすいミスとスムーズに進めるポイントも詳しく紹介
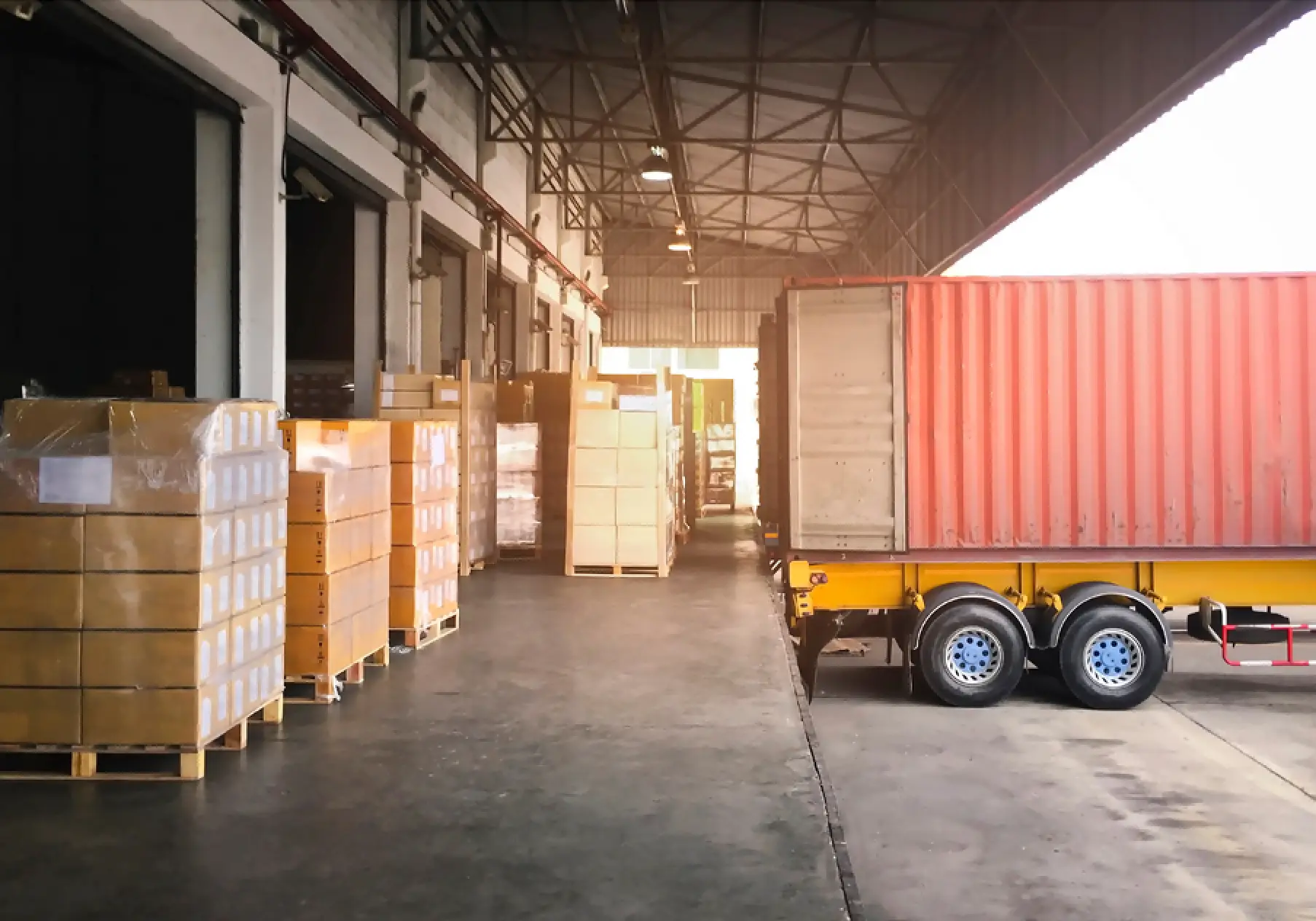
目次
出荷とは、倉庫から発送するまでに発生する作業のことです。注文から商品を送り出すまでの流れで、さまざまな業務があります。
本記事では、物流倉庫における出荷業務の概要・流れを紹介するとともに、生じやすいミスと業務をスムーズに進めるポイントについても触れていきます。
出荷とは
出荷とは顧客からの注文を受けて、その商品を倉庫から発送するまでの一連の作業プロセスのことです。
例えば注文の受領・商品のピッキング・梱包・配送準備などが含まれます。
出荷は、顧客が求める商品を効率的かつ迅速に届けるために不可欠であり、物流の効率性と顧客満足度の向上に直接影響を与えます。
出荷の流れ
ここからは、出荷業務の流れを紹介していきます。
1.出荷情報登録
注文内容(商品情報・数量・配送先住所)をシステムなどに取り込み、出荷登録を行います。
2.在庫の引き当て
注文された商品が在庫にあれば、その商品を注文に割り当てます。在庫が不足している場合は、追加調達や顧客への連絡などを行います。
3.ピッキング
引き当てられた在庫から、倉庫内で注文に応じた商品を集める作業です。効率的なルート計画に基づいて、作業員が倉庫内を移動しながら、注文された商品を選び出します。
4.検品
ピッキングされた商品が注文内容と一致しているか、また商品そのものに不具合がないかを確認します。品質に問題があれば訂正・管理を行います。
5.梱包
検品済みの商品を、商品が破損しないように適切な包装材料を使用するなど、安全に顧客に届けるための梱包を行います。
6.発送
梱包が終わった商品を配送業者に引き渡して、顧客への配送を行います。配送方法の選定、配送スケジュールの調整、追跡情報など、予定通り商品を顧客に届けられるよう管理していきます。
出荷の流れで生じやすいミス
出荷にはさまざまな作業があるため、細かく管理していないと人為的ミス発生の可能性があります。ここでは、出荷の流れで起こりやすいミスを紹介していきます。
商品内容の違い
出荷では、顧客が注文した商品と異なる商品を発送してしまうといったミスがあります。
商品内容の違いが起こる原因の一つに、ピッキングの際に、色やサイズ、品番を間違えてしまったりなどがあります。
商品内容の違いは、顧客満足度を大きく損なう可能性が高いため、特に注意が必要です。
商品数の違い
出荷では、注文された数量と異なる数の商品を発送するミスも考えられます。例えば、ピッキング時のカウントミスや検品時の誤りにより発生することがあるでしょう。特に商品の数量が多い場合、数量を誤って数えてしまう誤出荷が考えられます。
注文した数と違う数量が届き、さらに不足分があった場合、顧客満足度の低下に直結します。過剰に入っていた場合、顧客は混乱するかもしれません。
送り先の違い
商品の内容が合っていた場合でも、誤った配送先に送ってしまうミスも考えられます。
例えば、受注データの入力ミスや、何らかの理由で梱包・発送時のラベルの貼り違えが起きてしまったことなどが原因で起こる可能性があります。
送り先の違いは、顧客に直接影響を与え、信頼性も低下します。
付属品の入れ忘れ
付属品の入れ忘れとは、例えば取扱説明書や保証書、必要な部品など、商品の付属品を梱包する際に入れ忘れてしまうミスのことです。発生する原因として、商品の付属する点数の確認不足だったり、誤って他の商品に部品を梱包してしまったなどが考えられます。
顧客は商品が届いても付属品の入れ忘れがあると、すぐに商品を使用できない、などといったストレスを感じてしまいます。
検品不足商品の出荷
検品不足商品の出荷とは、損傷や不良がある商品を、検品プロセスで適切に検出できずに出荷してしまうことです。
例えば検品作業の担当者のミスで、商品の破損・汚損などに気づかないまま、正常な商品として処理してしまうなどといった品質管理の不備により、この問題が発生します。
検品不足商品を発送してしまうと、顧客の不満を招き信頼を失います。
出荷の流れをスムーズにするポイント
ここまで、出荷の流れと起こりやすいミスを説明しました。ここからは、出荷の流れをスムーズにするポイントについて紹介していきます。
作業プロセスの自動化
物流倉庫において、ピッキングや梱包・出荷時の品質チェックなど、ミスが発生しやすい作業を自動化すれば出荷作業の効率向上を期待できます。
例えば、バーコードスキャナーやRFIDタグを用いたピッキングシステム、自動梱包機を導入すれば、ピッキングや検品、梱包作業において、人によるミスを削減できるでしょう。
新規で機器を導入するときは、作業員のスキルと経験に合ったものであること、使用する前に適切なトレーニングを実施するようにしましょう。
適切な在庫管理
出荷の流れにおいて、在庫の過不足により、出荷の流れが停止してしまうことがあります。
例えば、在庫が不足していると、商品の出荷が遅れてしまい顧客が希望する納期に商品を届けられない可能性があります。在庫が多すぎると、ピッキングの際に、対象商品までの動線が妨げられて、対象の商品の取り間違えのリスクもあります。
そのため、リアルタイムな在庫管理ができるシステムやサービスを導入して、正確な在庫数を維持できるようにし、在庫過剰や品切れを防ぎましょう。
倉庫レイアウトの最適化
倉庫レイアウトの最適化とは、最も頻繁に出荷される商品が近くに配置される、注文から出荷エリアまでの動線がスムーズになるように、レイアウトを適切な形にすることです。
例えば、商品の種類やサイズに応じて、棚、ラック、パレットなどの保管方法を変更する、なども最適化の方法の一つです。また、効率的なピッキングと移動が可能になるように、通路を調整することも重要です。
倉庫レイアウトを最適化することで、出荷の流れをスムーズにできるでしょう。
出荷の流れを改善したいなら、TS-BASE 受発注がおすすめ
本記事では、出荷の流れについて紹介しました。
出荷の流れを改善したい、倉庫担当者のオペレーションを改善したい、人為的なミスを防ぎ出荷業務の効率を上げたいなら、TS-BASE 受発注の活用をおすすめします。
TS-BASE 受発注では、倉庫管理システム(WMS)の機能を有する「倉庫システム」を利用することで、受注から発送までを一つのサービスで完結します。出荷の流れにおいて重要な、在庫数・出荷状況の確認をシステム上で行え、倉庫業務における業務効率化を実現します。
TS-BASE 受発注の倉庫管理機能について詳しく知りたい方はこちらの資料もご覧ください。
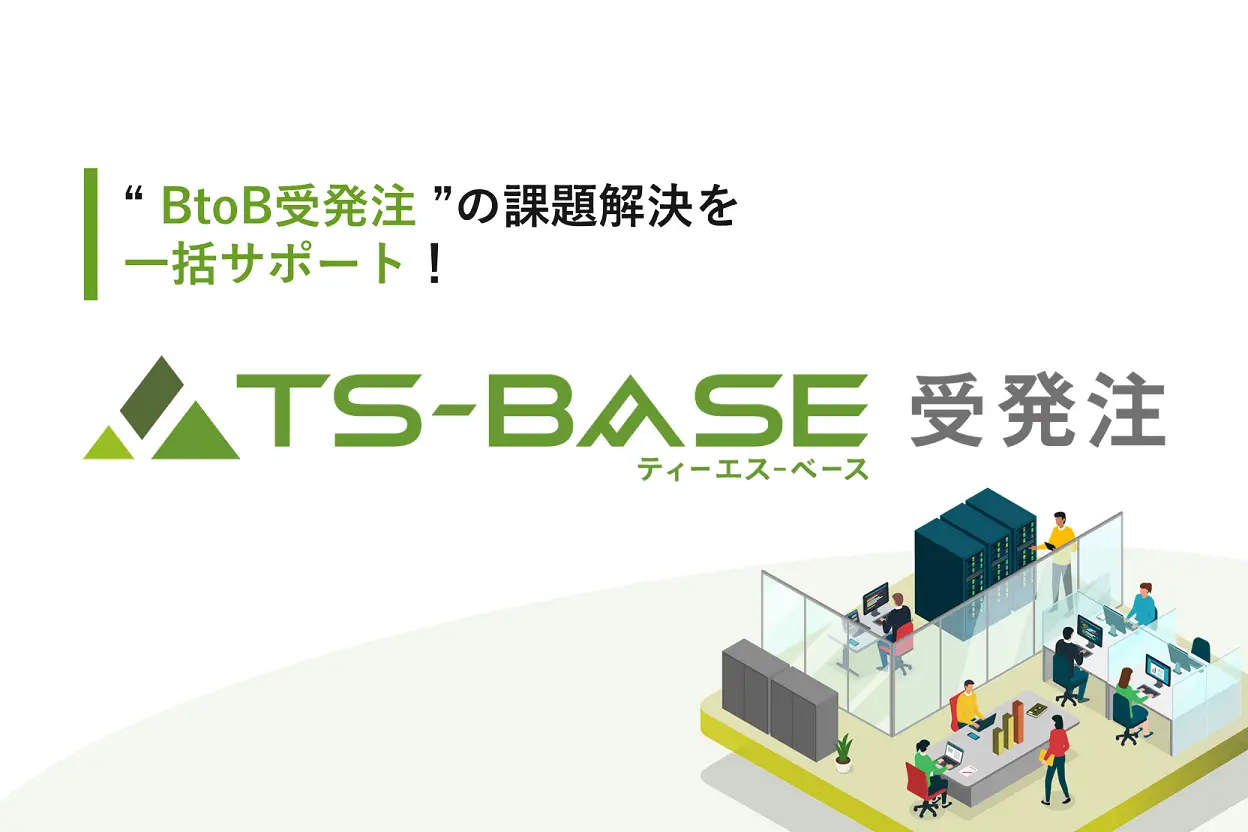
-
TS-BASE編集部さん
TS-BASEシリーズの促進を目指し活動しています。
導入をご検討の方は
こちらから
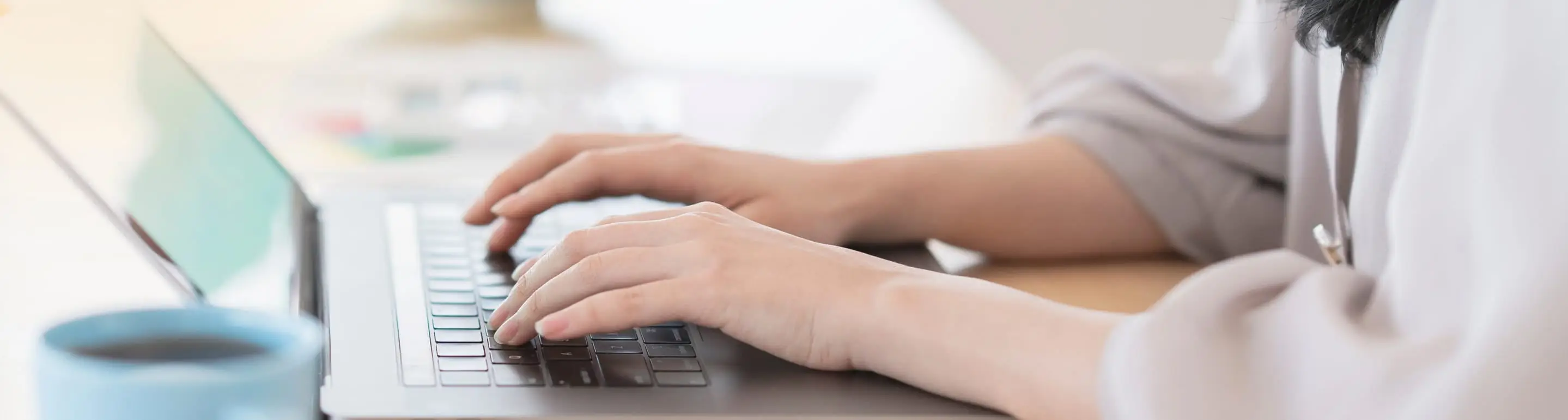
-
サービスの紹介資料や
お役立ち資料は
こちらから -
導入のご検討やその他ご相談は
こちらから