株式会社ユニバンス
製造現場に導入した「誰でも簡単に」操作できる注文システムで生産性が向上
- 製造
- TS-BASE 受発注
- 受発注業務の効率化
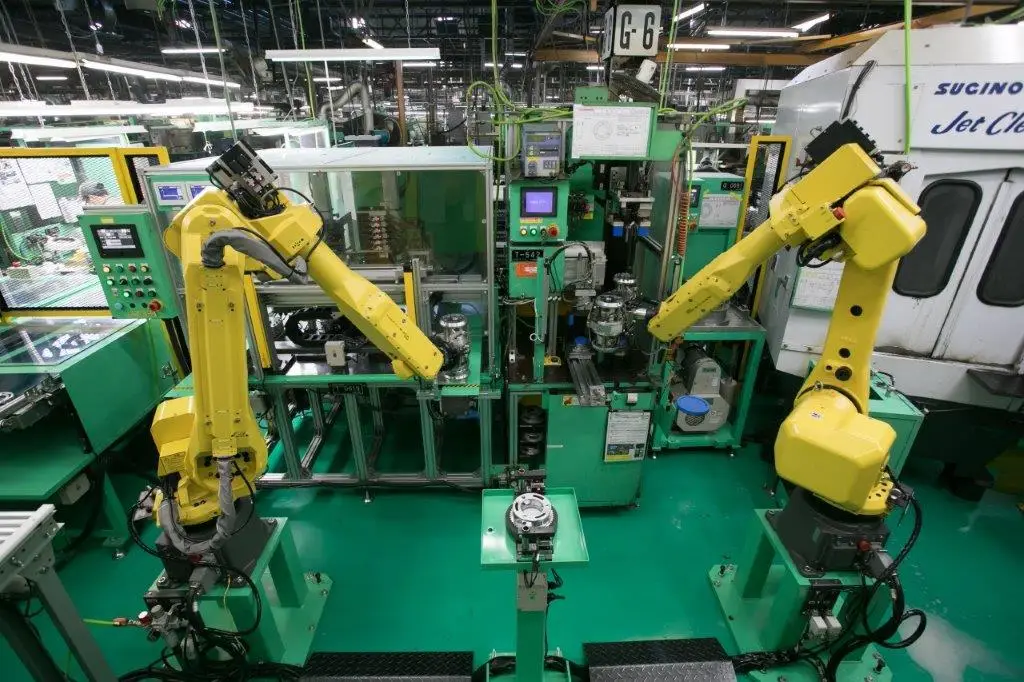

株式会社ユニバンス
生産管理部 グローバル生産管理グループ課長 山下 忠宣さま
自動車の駆動系部品を専門に扱う専門メーカー「株式会社ユニバンス」。設計・開発から生産まで一貫して行っている「駆動系ユニットメーカー」は世界でも数少ない。現在は、更なるクオリティ向上や競争力強化のために海外現地化を推進。ユニバンス独自の技術を生かした4つの主要事業を中心に、各国のニーズに的確に応えるサービスを展開している。
- 課題
・さまざまな外部環境の変化やニーズへの対応。
・お客さまからの内示情報と発注数の乖離。
・材料在庫数が要因の機会損失や問題が増加。
・その時の状況に対応できる、新たな運用の確立。
- 施策
・その時の状況に合う材料発注を製造現場の従業員が行う。
・「誰でも簡単に」操作できるシステムの導入。
- 結果
・TS-BASE 受発注を活用した社内受発注の運用を開始。
・TS-BASE 受発注の注文データと既存ERPシステムの連携。
・在庫の最適化により生産計画がスムーズに遂行される。
・簡単な操作説明会の実施のみで運用を開始できた。
・「誰でも簡単に」操作できる注文サイトは、スムーズに浸透。
自動車部品などの製造を行う「株式会社ユニバンス」では、社内受発注業務に「TS-BASE 受発注」を導入している。製造現場と生産管理部をつなぐ架け橋としてシステムを導入した経緯は、外部環境の変化に追従できていない危機感だった。同社が、新たなシステムの導入を検討したプロセスや、「誰でも簡単に」を目指した理由などを、生産管理部 グローバル生産管理グループ課長 山下 忠宣さまへ話を聞いた。
自動車部品の供給を行うユニバンス
株式会社ユニバンスは、静岡県湖西市に本社拠点がある「自動車部品などの製造および販売」事業を行っている企業だ。国内にある3つの工場では、電気自動車・ハイブリッド自動車用のギヤボックスや、駆動力に欠かせないトランスファーなど、数多くの製品・部品を生産。独自の開発力と技術力を駆使したプロダクトは、日本のものづくりを支える立役者として、多くの企業からの支持を得ている。
注釈:同社の技術が凝縮されたプロダクト。向かって左から、トラック用モーター・ジェネレーター用ギヤボックス、パーキングロックシステム付ギヤボックス、パートタイム4WDトランスファー。
同社生産管理部の山下さんは、取引先企業からの製品発注を取りまとめ、生産計画の策定や材料の手配を行うなど、安定した製品供給に不可欠な役割を担う人物だ。独自の資材所要量計画を仕組化したシステムをベースに、お客さまの需要に応じた対応をしてきた。しかし、ある出来事をきっかけに、強い危機感を抱くようになっていった。それは、突然訪れた疫病の流行だった。
ニーズに対応する「新たな仕組み」が必要になった理由
2020年から流行した「新型コロナウイルス感染症」の影響は、同社にとっても大きなものだった。「半導体不足などを含む、絶えず変化する市場に対応するため、新たな仕組みづくりが必要になった」と、山下さんは話す。
以前は、独自のERPシステム(生産管理や在庫調整などの役割で活用されているシステム)が、必要材料を自動で算出し発注を行う仕組みが採用されていた。過去のデータからも、お客さまからの内示情報に近い数量が実際にオーダーされていたため、生産管理部のメンバーは、自動算出する数量通りの材料を手配し、製造ラインでの生産も滞りなく行われてきた。
長年かけて築き上げた仕組みが揺らいだのが、コロナ禍の訪れだった。内示情報と実発注数との乖離が要因で、材料の過剰在庫などが発生。生産活動に大きな支障をきたすケースが増加していったのだ。
「当時、このままだと外部環境の変化やニーズに対応できない…。という危機感が本当に強かったです。そんな、今までのパターンが通用しない状況下で、最も信頼できたのが製造現場にいる仲間でした。
この瞬間に最適な”さじ加減”ができる現場感を取り入れて、『誰でも簡単に注文ができる環境』を構築できれば、危機を脱することができるのでは。そうすることで、円滑に回るようになるのでは。と、考えました。
そんなことを思っている時に、たまたま飲食店で目に留まったものが、結果的にTS-BASE 受発注との出会いにつながっていったのです」(山下さん)
焼肉屋での何気ない行動がカギに
イメージ画像 出典:Shutterstock
「たまたま行った焼肉屋さんで、『タブレットを使用して、メニューを選択し、注文ボタンを押す』という行動をしたんです。その時に、こういう仕組みをベースにしたら、誰でも簡単にできそうだと思いました。その後、適合するソリューションを探し始めました」(山下さん)
以前は一部の企業しか取り入れていなかったセルフオーダーシステムも、コロナ禍が長期化するにつれて一般化していった。そして、通信販売利用者の増加もあいまって、通信機器を介した注文行為に抵抗を感じる人が少なくなっていたのだ。
そこに着目した山下さんは、「製造現場のメンバーに注文してもらう」「誰でも簡単に操作できる」「注文データと既存ERPシステムの連携」の3軸に適応できる仕組みを調査していった。
誰でも簡単に操作できるプロダクトは目に留まるが、「基幹システムとの連携」のキーワードに高いハードルがあった。そんな中、内容面でも予算面でも現実味があったのが、「TS-BASE 受発注」だったという。
「実際は厳しい部分もあったと思いますが、TS-BASE 受発注の営業さんが、弊社の要望を親身に聞いてくださって、道筋を示してくれたことが大きかったです。『誰でも簡単にできる』というイメージも明確にもてましたし、TS-BASE 受発注は、目的の3軸を満たすシステムだと思い決定いたしました」(山下さん)
操作説明会が不要だった「TS-BASE 受発注」
導入後、まず実感したのが、「詳しい説明がなくても、大体の人が操作できる」点だった。新たに導入した「TS-BASE 受発注の注文サイト」は、多くの製造メンバーに使用して欲しいものだ。山下さんは、操作説明会や理解を深める勉強会の開催などを視野に入れ、普及に努めようと考えていた。
注釈:「TS-BASE 受発注 注文サイト」の操作画面イメージ。通販サイトのような見た目で「直感的に操作ができる」と好評だ。
しかし、予想とは反して、現場監督など中心メンバーに操作説明を行い、手順書を配布した後は、製造現場の従業員同士が助け合いをして自然に浸透していったという。そして、1年以上が経過した現在も、説明会や勉強会の開催はしていない。
この件以外にも、製造現場のメンバーには、「頭が下がる思いだ」と山下さんは話す。
「現場の感覚を取り入れるという点は、注文サイトを活用することで、円滑な生産に直結したという実感があります。現場からは、『在庫への意識が高まった』など、前向きな感想はもらっていますが、業務工数が増加してしまったことは事実です。
あと、TS-BASE 受発注の導入後、新たな発見がありました。我々管理部の想像をはるかに超える『少量在庫』で、現場が回っているんです。思わず、大丈夫だろうか…と思う数量なんですよね。でも、結果を見る限り、製造のタイミングを加味した『最適な在庫』なのだと思います。
率直に、製造メンバーの現場感は『卓越しているな』と思っています。驚きと感謝の気持ちでいっぱいです」(山下さん)
同社では、部署を越えた情報の見える化を推進しようとしている。「必要な時に、必要な情報を、必要な人に届ける」を実現することで、今回のような業務改善に直結する新たな気付きが生まれるはずだ。それは、お客さまのニーズに応えた、最適な製品を提供することへとつながっていく。そのためにも「誰でも簡単に」というキーワードは、今後も重要になっていくのだろう。
導入をご検討の方は
こちらから
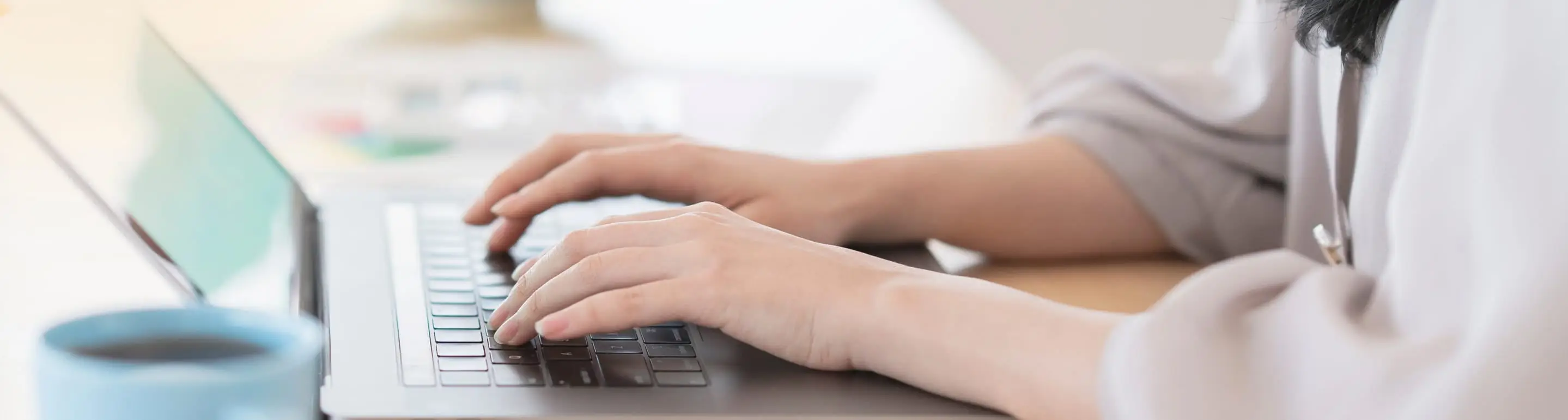
-
サービスの紹介資料や
お役立ち資料は
こちらから -
導入のご検討やその他ご相談は
こちらから